How We Automated Waste Management at DB Schenker’s Irish Distribution Centre
LSM partnered with Wheel.me, a Norwegian smart mobility company, to implement automated waste management at DB Schenker’s 220,000-square-foot distribution centre in Ireland. The collaboration addresses key goals in operational efficiency, safety, and sustainability.
Wheel.me’s Genius 2 wheels transform ordinary objects into autonomous, mobile robots, allowing facilities to optimise labour and improve process efficiency. This expertise in robotic movement and intelligent navigation provided an ideal complement to LSM’s advanced waste balers and compactors.
How the Collaboration Began:
LSM identified an opportunity to integrate Wheel.me’s technology to streamline waste management in large facilities. Challenges such as labour shortages, safety risks, and stringent environmental regulations made automation a key solution. With a strong record in autonomous mobility, Wheel.me became the ideal partner to help LSM create an automated waste management system, beginning with DB Schenker’s Irish facility.
The Problem:
DB Schenker’s previous waste-handling process required operatives to transport 30 large bins of waste to LSM balers. This was a labour-intensive routine that led to bottlenecks, health and safety risks, and inefficiencies. The client aimed to optimise labour, improve safety, and lower environmental impact by reducing the frequency of waste collection.
The Solution:
Step 1: Designing and Retrofitting the Carting System
A standard 1,100-litre bin typically comes with castor wheels that are not autonomous. LSM took a unique approach in designing a custom carting system that allowed Wheel.me’s Genius 2 wheels to transform standard 1,100-liter bins into autonomous transport units. This single adjustment allowed the bins to navigate independently to the LSM H50 balers for compaction.
Wheel.me’s Genius 2 wheels are designed to be compatible with almost any object, but for this use case, LSM positioned the mounting brackets in identical locations on each bin. This precise placement ensures that the balers can automatically pick up each bin for emptying, eliminating the need for manual intervention. The Genius 2 wheels were calibrated to withstand the structural demands of fully loaded bins (up to 1,100 litres), including stability across various surfaces and smooth handling to prevent damage during the bin-raising and lowering processes.
The distribution centre has three distinct ground surfaces between the waste areas and the balers, requiring the Genius 2 wheels to transport bins safely and stably across both wet and dry conditions.
Step 2: An Automated Waste Management Workflow
Once the bins were compatible with the Genius 2 wheels, LSM moved to integrate the system with its H50 balers. A wireless interface, or “wise unit,” was developed by LSM to enable communication between the robotic wheels and the balers. This Wi-Fi-enabled interface allowed the balers to “recognise” when a Genius 2 bin was ready to be emptied.
A color-coded lighting system provided real-time status updates to operators in the baling area, adding an extra layer of safety to the Genius 2 system’s built-in sensors and collision-prevention cameras. The lighting signals include:
- Green: The baler is ready for a bin to be delivered.
- Red: The baler is in motion, and no bins should enter or leave.
- Blue: The bin has been emptied and compacted, allowing Genius 2 to transport the empty bin away.
This closed-loop communication and signalling system enhances safety and efficiency by coordinating each stage of the process.
Step 3: Custom Bin Lifts and Enclosures
To integrate smoothly with DB Schenker’s infrastructure, LSM designed a custom H50 Rear-Filling Clamped bin lift and an enclosure specifically fitted to the site’s levelling dock. This setup enables the balers to handle the bins autonomously, removing the need for workers to manually move bins into position.
This automated waste management solution has significantly increased efficiency:
- Enhanced Safety: Automation and the closed loop system minimises worker exposure to waste materials, reducing health risks.
- Cost Savings: By implementing autonomous driving waste bins, DB Schenker could avoid hiring two FTE and estimate a cost avoidance of around around € 80,000 per year.
- Optimised Labour: The process has freed up approximately 3–4 workers for other essential tasks.
- Space Efficiency: only 7 bins are now needed onsite instead of the previous 30.
This partnership showcases how LSM’s innovation in waste management solutions, enhanced by Wheel.me’s autonomous mobility technology, offers clients a practical path toward safer, greener, and more efficient operations. Through continued collaboration, LSM and Wheel.me are set to deliver similar solutions to meet the needs of more of LSM’s global clientele.
Interested in Automating Waste Management at Your Facility?
If your high-processing site faces similar labour-intensive waste management challenges, contact LSM today. We’ll work with you to create a customised solution powered by Wheel.me’s robotic technology to automate waste management operations, improve safety, and reduce costs. Let us help tailor a solution that works for your business.
Want to discuss your baling needs?
Talk to a DistributorKnow which baler is right for you?
Get a QuoteTrusted Around The World
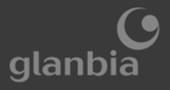
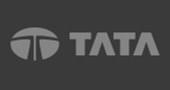
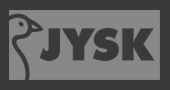
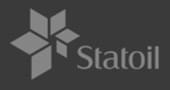
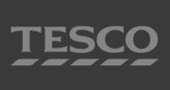
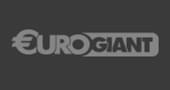
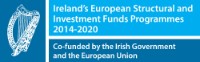
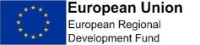