Performance
BUILT TO LAST
LSM products embody more than 20 years of quality engineering, focused innovation and proven performance. That’s why our balers work, every time, every day.
Why Choose LSM?
Engineered Reliability
We design and manufacture LSM machines at our state-of-the-art
facility in Portlaoise, Ireland, using only top-quality, European-made
parts. Precision lasers cut components from flat plates, creating
stronger, longer-lasting parts than typical box section cuts.
Powerful Performance
Our unique, industry-leading dynamic power technology helps us
deliver dramatic savings of energy, time and cost. We call it e-Power,
and it lets you power our small balers with a standard household outlet.
It also uses a larger motor more efficiently, giving you greater
compaction for greater density bales, so you can compact more waste
in fewer cycles.
Complete Solutions
Whether you need to bale cardboard, plastic, tyres or all three, at a
single location or across an international network, LSM can create or
customise a complete waste compaction solution for you. Our
machines are working in corner markets, five-star hotels, auto-body
shops and cruise ships all around the world.
Excellent Value
The full range of LSM balers is competitively priced, with both rental
and purchase options available from local distributors around the
world. The outstanding efficiency of our machines ensures added
savings of time, cost and energy, and easily sourced, high-quality
European made parts and components mean fewer, faster, easier
service and maintenance visits.
Ongoing Innovation
From engineering for increased efficiency to integrating greater safety
controls, LSM is committed to the design and manufacture of the most
reliable, best performing balers available. We rely on relentless
innovation to continuously improve our process—because we intend
every machine we make to last for years to come.
Green Advantage
Waste reduction and recycling isn’t just our business, it’s our way of life.
LSM takes all possible steps to reduce our own carbon footprint, using
modern laser-cutting and flat plates to reduce waste in manufacturing,
longer lasting parts, innovating dynamic power that uses less power to
achieve greater compaction, designing low voltage user controls that
require less power and are safer to use, and much more.
These machines just don’t break down. We have 52 LSMs, many in operation for 10 years with no new parts. And we give them hell! We’re processing over 350 tonnes each year. We’ve had others, these are the best.
Paul Kelly, Facilities Manager, Eurogeneral
Ready to cut costs?
Check out our guide to creating a more economical and efficient recycling process.
Download GuideWant to discuss your baling needs?
Talk to a DistributorKnow which baler is right for you?
Get a QuoteTrusted Around The World
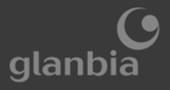
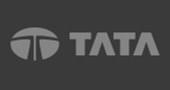
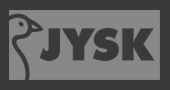
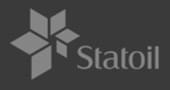
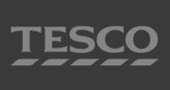
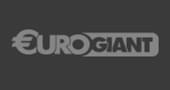
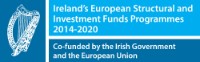
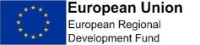